Secrets for Drying Fine Powders in a Vacuum Oven
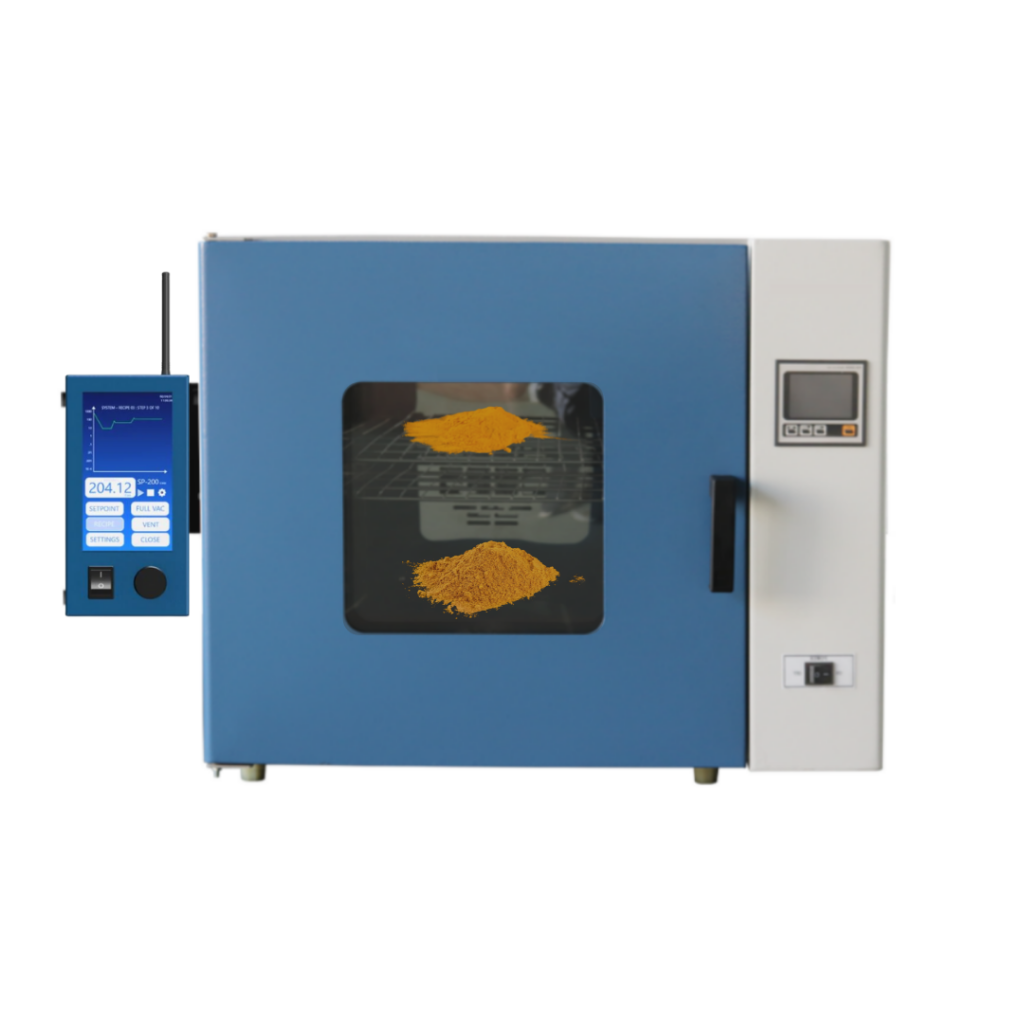
How do you Dry Fine Powders in a Vacuum Oven?
Most often powder drying applications involve the introduction of heat to a solution, wet powder or slurry. Then bulking and packaging of the dried powder usually follows. Common dryer types include tray, fluidized bed, spray, rotary and vacuum oven dryers. In any type of dryer, the dry powder can build up as a bulk or layer in various locations within the dryer, or in downstream process equipment like your vacuum pump. Fine powders building up in your pump and possibly in your lab can lead to issues with increased pump maintenance. Or, other potentially harmful issues if the powders make it out of the pump depending on what type of powders you are drying.
Vacuum drying is done in an airtight chamber connected to a vacuum pump. The vacuum oven utilizes a balance of temperature and vacuum pressure to reduce the humidity within the chamber and the product being dried. This technique is one of the most common laboratory, research and industrial drying techniques for heat sensitive, hygroscopic and/or toxic powders and granules. Industries that commonly dry powders include: pharmaceutical, food processing, plastics and chemical processing.
The Secret is Fine Control
Digivac comes to the rescue of process heating in your vacuum ovens by telling you our secrets for drying fine powders. The magic behind drying powders without creating a mess is two fold:
1. Controlled Bleed: Introduce a small purge of dry air or nitrogen to remove water vapor from the system. Bleed/Purge cycles will help speed up the drying process, but when drying fine powders this process can also flush out fine powders if the venting is not controlled. The SNAP offers both fine proportional bleed control and proportional throttle control with its novel patent-pending valve.
2. Controlled Vacuum: With drying fine powders slow and steady wins the race. The secret to success is to very gently apply the vacuum over time therefore avoiding the rush of air that can bring with it powdered material outside the dryer.
For example, create a ramp rate that will slowly reduce the level of vacuum in the oven chamber from atmosphere down to your desired pressure over a longer period of time, perhaps 10-20 minutes. The DigiVac SNAP vacuum controller allows you to customize recipes for pressure over time. This automated vacuum controller allows the fine powders to dry without any unnecessary disturbance.
For the purpose of this blog, we are going to focus on #2: Fine Vacuum Control by Starting Your Heat Processing with a RAMP.
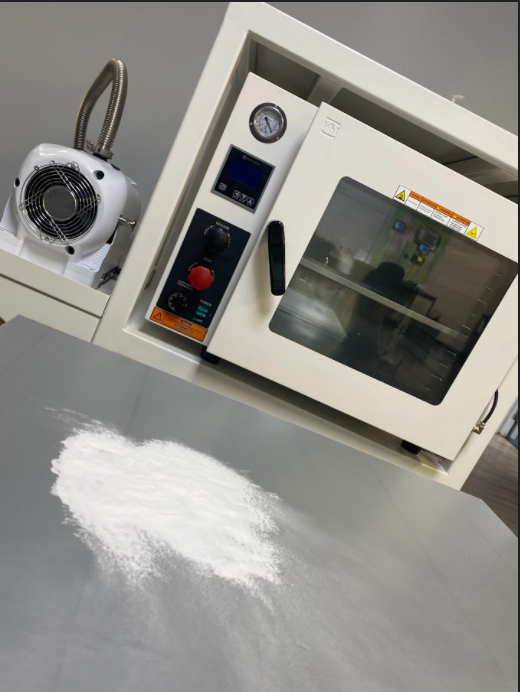
A ramp rate is the change of something over time, and in this case the change or pressure over time. A ramp rate of 10 Torr/minute means that the pressure changes gradually by 10 Torr over 60 seconds. For one of our customers drying powders, they chose a ramp rate of approximately -150 Torr per minute. They would start at 750 Torr, after a minute the pressure had gone to 600 Torr, then the next minute it was at 450 Torr…etc. until they reached their target pressure.
“gently apply the vacuum by avoiding the rush of air”
This is a very automated way to make sure that the powders don’t end up in your vacuum pump. It is based on being able to control the process more efficiently and will help optimize your processing time and lower the risk of blowing powders around your chamber or lab. Creating a ramp rate leaves much less room for error !
The Ramp Rate
Many vacuum ovens on the market have onboard temperature control, but manual vacuum control through isolation valves. A ramp over time is possible using manual isolation valves, but it is time consuming and is open to operator error. Adding an automated vacuum controller like the SNAP will help you with automation and optimization, ultimately creating a more repeatable and clean powder drying process.
Learn More About The DigiVac SNAP here